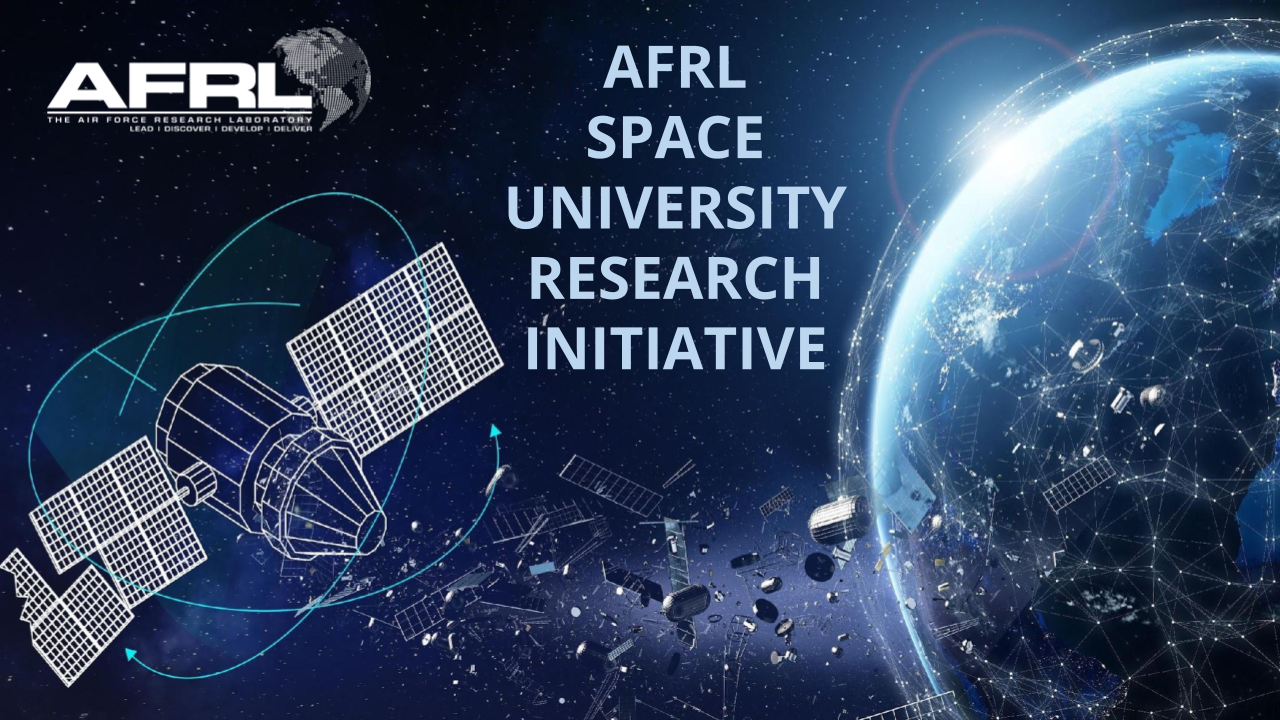
The SURI (Servicing and Utilization for Responsive In-Orbit) Project, conducted by the AGMAN Lab, addresses key challenges in enabling long-term operation and sustainability of space assets through robotic on-orbit servicing. This ongoing research aims to develop intelligent and agile systems that can safely inspect, maintain, and modify satellites or structures in space. The project spans several critical domains, with current focus on dexterous on-orbit maintenance, emphasizing safe interaction under uncertain dynamics.
Core Components of the SURI Project:
1. Intelligent Inspection
Utilizing multi-robot systems and adaptive estimation techniques, SURI enables safe, autonomous inspection of spaceborne structures—even when surface friction or object dynamics are unknown. These inspections are critical for identifying damaged or jammed components such as solar panels or antennae.
2. Dexterous On-Orbit Maintenance
A primary focus of SURI is safely dislodging and manipulating stuck or malfunctioning satellite components using robotic arms and collaborative tugs. This task involves:
2.1 Generating Dislodging Motions from Kinematic-Dynamic Models:
The system models the joint-space dynamics of jammed hinges or appendages using Euler-Lagrange formulations, accounting for unknown stiffness, damping, and contact friction. These models inform control strategies to initiate safe dislodging with bounded forces.
2.2 MPC-Based Grasp Planning for Contact Force Regulation:
To support reliable physical interaction, the project employs a robust adaptive model predictive control (MPC) framework with online set-membership parameter estimation. This approach enables the robotic system to adapt in real time to changes in system properties—like hinge friction or grasp alignment angle—while ensuring safety constraints are met.
2.3 Trajectory Optimization Under Actuator Constraints:
By incorporating actuator bounds and uncertainty-aware state constraints into the MPC pipeline, the system generates feasible, smooth motion plans that guide the manipulator from initial grasp to the target pose, without overexerting joints or causing collisions.
3. Agile On-Orbit Manufacturing
As an extension of dexterous maintenance, the SURI platform is being evaluated for its potential in on-orbit fabrication and assembly, where precise force-controlled manipulation and coordinated multi-robot action are essential for constructing or modifying structures in microgravity.
Current Work and Future Directions
The AGMAN Lab is actively developing the theoretical control architectures and validating them through hardware-in-the-loop experiments, including planar dislodging tasks and 3D multi-agent simulations. Future milestones include the integration of vision-based grasp inference and experimental validation aboard reduced-gravity platforms. For more information see https://longsengao.com/projects/1_project/